FMEA & you save
No errors, no costs
Increase reliability of production and products
Reduce costly, reactive corrective actions
Targeted communication – both internally and externally
Our Failure Mode & Effect Analysis
Permanent optimization for error-free processes
Errors cost money. Therefore, it is important to predict errors before the start of a product development or a process and to be able to nip them in the bud. This is where FMEA (Failure Mode and Effects Analysis) comes into play.
This analysis is team-oriented and is intended to expose potential errors or their causes in products, in their use or in processes in advance. If possible errors are found, their significance must then be recognized and evaluated in order to be able to initiate optimum preventive measures as required.
In the best case, high follow-up costs can be avoided or at least reduced.
This is how we reduce the susceptibility to errors
Our FMEA software for products & processes
In general, the goals of the impact analysis are derived from the goals of the respective company. Thus, customer demands, but also increased quality requirements have at least the same effect on the analysis as possible necessary cost optimization of products and processes. Here, the company goals for quality & risk management are concretized and thus developed into action goals.
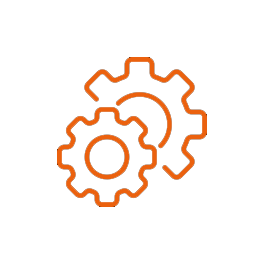
System-FMEA Product
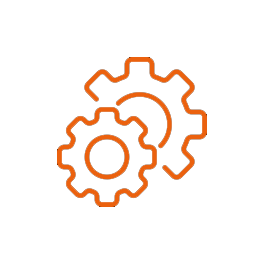
System-FMEA Process
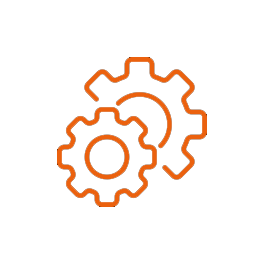
Hybrid-FMEA
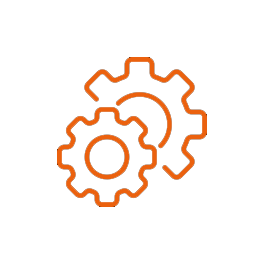
FMEA VDA AIAG
Frequently asked questions about FMEA
FMEA is used in product development (product FMEA) and in process development (process FMEA). In product development also spoken of design, D-FMEA or construction FMEA. In production or manufacturing processes, FMEA is also known as process, P-FMEA or service FMEA. The logical procedure is always based on the same approach.
The FMEA offers an early detection and evaluation of possible defects already during the design or process planning phase. In doing so, you draw on the experience of product or process FMEAs that have already been created.
In the automotive industry, software for FMEA is now required. In other industries, software is not required, but even here a software solution supports you by performing the FMEA faster with more transparency.
The FMEA is a systematic and proven method for ensuring required product properties. In connection with other modules, which make the errors and deviations directly available to the FMEA for further processing, you determine the causes and introduce targeted measures for error prevention. This provides you with a knowledge repository for future projects.
With the 7th step of the FMEA – AIAG/VDA harmonization, you create the summary in the form of a report for project management / management.
This contains practical information on technical risks of error, measures to be introduced and costs.